Powder coatng is applied on ACP sheets,wheel trims, vehicle frames, appliancs such as vending machine, microwaves,agricultural equipment and many more items. Powder coating is a durable finish which is applied to most of the industrial manufactured products to protect from corrosion.
Powder coating is a finely groundmaterial which is applied as dry finishing on products. Powder coating consistsof resin, pigment of colour, and additives for gloss or matt finish. The film of powder is electrostatically applied with the help of electrostatic spray gun and later on it is treated with heat. Heat is applied in thermoplastic and thermosetting powder coatings to solidify the coating on the surface. The sturdiness of the powder coating depnds on the warming limit of the fuel.
Factors To Be Considered During Powder Coating
Temperature Control
For powder coating, specific temperaturecontrol is crucial so that the coating arrives at the surface at full fix andsets up the whole film properties at the intended surface. This process is done carefully for the Powder and Liquid relieving process so to control it, uniform temperature control is extremely important. It is done with a working spacebroiler.
Uniform Heating
Uniform heating and controlledtemperature are important in the application of powder coating. Use a superiorgrade LPG cylinder to heat the fine film of powder on the surface to provide a tough and smooth finish. The LPG cylinder provides better flame for heating compared to Light diesel or High diesel oil and other solid fossil fuels.
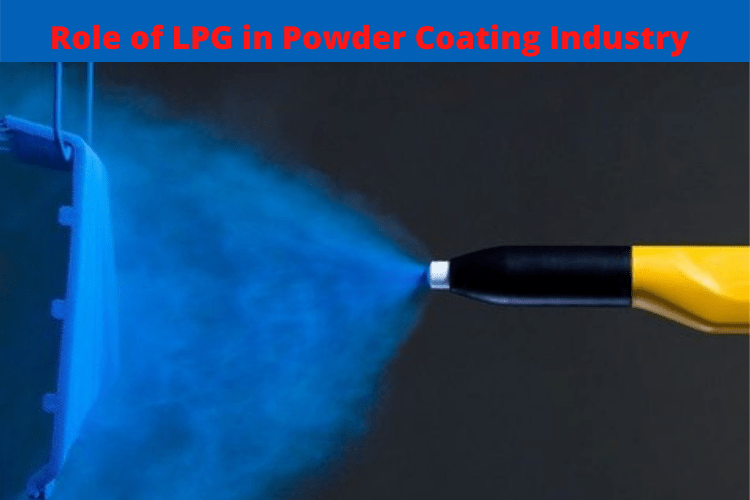
Advantages Of Powder Coating
1. Powder coating is a thermoplastic coating reused and recycled. Moreover, powder coating is done with temperaturecontrol on the surface that ensures it does not lead to too much wastage.
2. Powder coating is made from non-toxicmaterials which dos did not pose much threat to workers working in powdercoating factories.
3. It measures few preferences overordinary fluid coating. Powder coating has expanded sturdiness, quicker turnaround time, lower material expenses, and less natural effect.
4. Powder coating is more cost-effectivethan ordinary powder coating and more durable than other alternatives.
5. Powder coating is applied for afinished look on metal. It repels moisture, chemicals, and other materials thatlead to the oxidization of metal.
Why You Should Choose LPG?
The need for broiler and heating ofcoating at high temperature is generally met by combustion through fossilfuels. However, fossil fuels are harmful to the environment as they release smoke emit toxic gases and particulate in the air. Whereas LPG is a cleaner and sustainable fuel that helps meet all energy requirements in the powder coatingindustry. Visit nearby private gas company in India for regular supply ofcylinder in powder coating industry.
Other Advantages Of LPG In PowderCoating Industry
Low Carbon Formation
LPG limits the emission of poisonous andcancer-causing substances in the environment that lowers the carbon formationin the powder coating industry.
Cost-effective
LPG gas company in India providescost-efficient gas. This is cost-effective than other fossil fuels. It helps infinance management in the small powder coating industry and provides enough energy for powder coating.
Environment Friendly
LPG cylinder is an efficient source ofenergy that has a lesser impact on the atmosphere and environment. LPG does notemit back carbon and it does not spill. It helps in improving the air quality and reduces the emission of harmful greenhouse gases.
Conclusion
LPG helps in uiform coating and energyefficiency in powder coating industry. LPG agencies provide unadulterated LPGfuel to ensure maximum productivity.